The journey of stone from the Quarry to the Customer
- Did you know that these magnificent granite stones are nothing more than chunks of rock that have been formed over millions of years?
- When magma or lava cools and hardens under immense pressure beneath the earth's crust,(about 50 km from the earth’s surface) these miraculous creations emerge.
- These are known as igneous rocks, and they cover the majority of the earth's surface. These rocks are robust and dense because the process occurs slowly over time.
- A big portion of granite has feldspar, a good amount of Quartz, and a small percentage of Mica and Amphibole. Granites come in a variety of colors according to the varying quantities of minerals contained in the stone. If the granite contains 20% quartz, it is considered pure.
- Granite is a term used in the commercial world to describe any hard stone that isn't marble. Diorite, andesite, syenite, anorthosite, basalt, and granulite are examples of igneous rocks that are typically marketed as granite.
- The granites with amazing colors can be seen predominantly in India, Brazil, and Norway
We start from where Nature has finished
Mining the rocks from quarries
Our journey begins with the removal of overburden, which is soil or gravel on top of the granite; unwanted stones are removed by drilling and blasting.
The next step is to carefully examine the right material from the quarry (a large number of natural rocks), and we surface and shape the stones into cubes or rectangles using drilling machines.
To complete the operation effectively and swiftly, we employ advanced technologies. These massive slabs of stone are broken into small rectangular chunks and sent to our warehouse for further processing.
The next step is to carefully examine the right material from the quarry (a large number of natural rocks), and we surface and shape the stones into cubes or rectangles using drilling machines.
To complete the operation effectively and swiftly, we employ advanced technologies. These massive slabs of stone are broken into small rectangular chunks and sent to our warehouse for further processing.
Transforming Stones to Slabs
By using a giant gang saw, the enormous rectangular blocks of stone are sliced into multiple slabs of similar size and thickness. The gang saw is made up of hundreds of evenly spaced parallel blades that produce slabs that are 2 to 3 cm thick and 9x6 feet in size (on order 4 to 30 cm).
The slabs are then polished on one side, bundled together with slabs from the same block, loaded into containers.
The slabs are then polished on one side, bundled together with slabs from the same block, loaded into containers.
Processing Unit
Chipping is used to separate all of the slabs, and then the individual slabs are transferred to an edge cutting machine, which meticulously trims the edges into the proper form before sending them to the next step.
The stone's blemishes, grainy surface, and undesirable lines are removed by the grinding machine, leaving it with a gleaming polish.
The stone's blemishes, grainy surface, and undesirable lines are removed by the grinding machine, leaving it with a gleaming polish.
Resining
To make the granites more desired and appealing, they are colored and given patterns. There are hundreds of colors and patterns to choose from, and we match color and texture to our customers' preferences.
These polished and colored granites may still include minor fractures, tiny holes, and structural flaws that diminish the granite's beauty and durability.
These flaws are addressed by heating them and applying Epoxy Resin. The slabs are then reheated to ensure that the epoxy Resin is fully absorbed.
To get the greatest finish, epoxy chemicals are combined with the appropriate color combination.
These polished and colored granites may still include minor fractures, tiny holes, and structural flaws that diminish the granite's beauty and durability.
These flaws are addressed by heating them and applying Epoxy Resin. The slabs are then reheated to ensure that the epoxy Resin is fully absorbed.
To get the greatest finish, epoxy chemicals are combined with the appropriate color combination.
Polishing
This is the final phase where any excess Epoxy Resin is removed and the surface is polished to a mirror-like perfection using an abrasive polishing machine. Finally, the scintillating polished granite makes us forget all our hard work and just admire nature’s miraculous stones.
We embellish various finish types that suit different requirements and usage. To name a few,
1.Swan Finish
Swan finish gives a rough matt look to the granite and it is created by sawing with diamond wire or diamond disc teeth mainly used in constructing pathways, steps, and driveways.
2.Glossy/Polished Finish
This gives a glossy mirror-like smooth finish highlighting the colors and patterns. Diamond pads are rubbed to obtain zero porosity. These granites can be used in granite countertops and vanity tops
3.Honed Finish
Honed finish produces a smooth surface with a matt finish, which is commonly used in bathrooms, kitchens, and pool flooring.
4.Flammed Finish
The granite is subjected to high temperatures and instantly cooled in the flammed finish. This process causes certain grains to rush up, resulting in a non-porous and rough surface. These granites are mostly employed in the construction of walkways and stairs
5.Antique Finish/Lapatura Finish
To get this finish, the granite is first lathered and then polished on heights to achieve a stunning appearance. The granite appears to be semi-rough and semi-smooth. For this reason, steel grey, the black pearl, and tan brown are recommended.
6.Shot Blasting
Shot blasting provides the stone a rough texture; each granite slab is blasted with minute iron beads at high speeds, causing it to lose its natural stone surface.
7.Sand Blasting
These granites were created by combining air pressure and water pressure with sand, ceramic beads, and abrasive chemicals. This granite is perfect for locations that require slip resistance, such as wet spaces and outdoor areas.
8.Bush Hammered
The top layer is pitted by machines to form a deep ridge giving a naturally rough texture that is mostly used for external walls.
9.Leather Finish
This kind has a leather-like finish, is smooth and matt, and is textured. It does not require sealing and is easy to maintain, making it suitable for restrooms, living rooms, and special tables.
We embellish various finish types that suit different requirements and usage. To name a few,
1.Swan Finish
Swan finish gives a rough matt look to the granite and it is created by sawing with diamond wire or diamond disc teeth mainly used in constructing pathways, steps, and driveways.
2.Glossy/Polished Finish
This gives a glossy mirror-like smooth finish highlighting the colors and patterns. Diamond pads are rubbed to obtain zero porosity. These granites can be used in granite countertops and vanity tops
3.Honed Finish
Honed finish produces a smooth surface with a matt finish, which is commonly used in bathrooms, kitchens, and pool flooring.
4.Flammed Finish
The granite is subjected to high temperatures and instantly cooled in the flammed finish. This process causes certain grains to rush up, resulting in a non-porous and rough surface. These granites are mostly employed in the construction of walkways and stairs
5.Antique Finish/Lapatura Finish
To get this finish, the granite is first lathered and then polished on heights to achieve a stunning appearance. The granite appears to be semi-rough and semi-smooth. For this reason, steel grey, the black pearl, and tan brown are recommended.
6.Shot Blasting
Shot blasting provides the stone a rough texture; each granite slab is blasted with minute iron beads at high speeds, causing it to lose its natural stone surface.
7.Sand Blasting
These granites were created by combining air pressure and water pressure with sand, ceramic beads, and abrasive chemicals. This granite is perfect for locations that require slip resistance, such as wet spaces and outdoor areas.
8.Bush Hammered
The top layer is pitted by machines to form a deep ridge giving a naturally rough texture that is mostly used for external walls.
9.Leather Finish
This kind has a leather-like finish, is smooth and matt, and is textured. It does not require sealing and is easy to maintain, making it suitable for restrooms, living rooms, and special tables.
Product Customisation
Our product range includes a wide range of Customized Printing Tiles, 3D Custom Print Tiles, Finally, the scintillating polished granite makes us forget all our hard work and just admire nature’s miraculous stones.
We provide customizations for
1. Tiles
2. Cobbles
3. Countertops
4. Gangsaw
5. Basalts
6. Tombstone / Monuments
We provide customizations for
1. Tiles
2. Cobbles
3. Countertops
4. Gangsaw
5. Basalts
6. Tombstone / Monuments
Our Machinery
Advanced and modern machinery is the backbone of Impex Granite, we have various machines that seamlessly support the complete lifecycle of Granites.
- Vertical Slab Multicutter
- Gangsaw from Friends Engineering Works
- Resining Line 45 from Friends Engineering Works
- Bhagwati machine and tools for Polishing
- Counter Top cutter from GTT & Co China
- For Shot Blasting Abrablast Shot Blasting Machine
- Thickness Calibration from Balaji Tools
- Cobbles Cutting Machine from New Engineering Tool
- Multi Cobble cutting machine with the capacity of 100 cubes/ min
- 7 Cutting Machines and 6 Single blade edge cut machine
- 4 Multi cutter machines
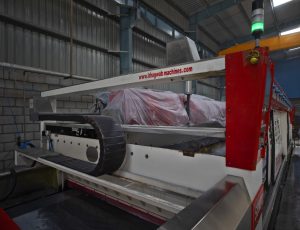
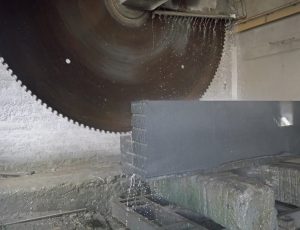
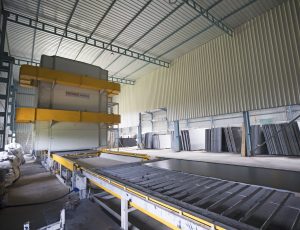
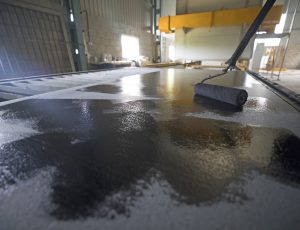
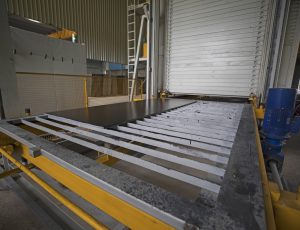
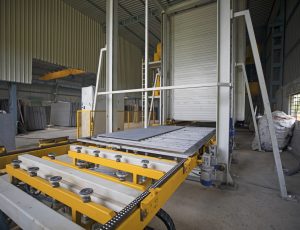
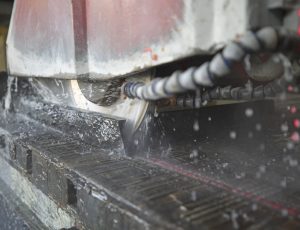
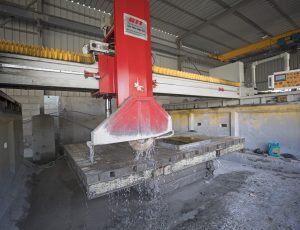
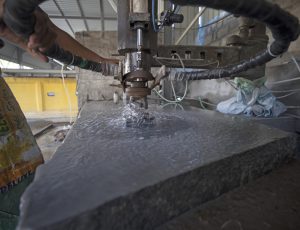
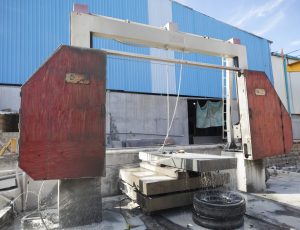
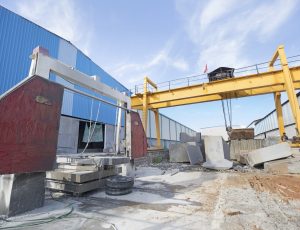
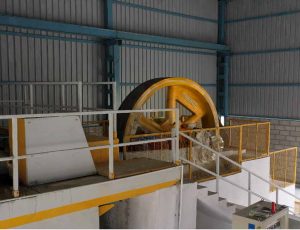
Previous
Next
Where do we mine the quarry?
Chamrajnagar Mysore is the location of our quarry mining unit. Our resource, who has over 30 years of experience, precisely selects the highest quality stones for the granite manufacturing process.
Packaging
All granite slabs that are ready to be shipped are packaged in wooden pallets.